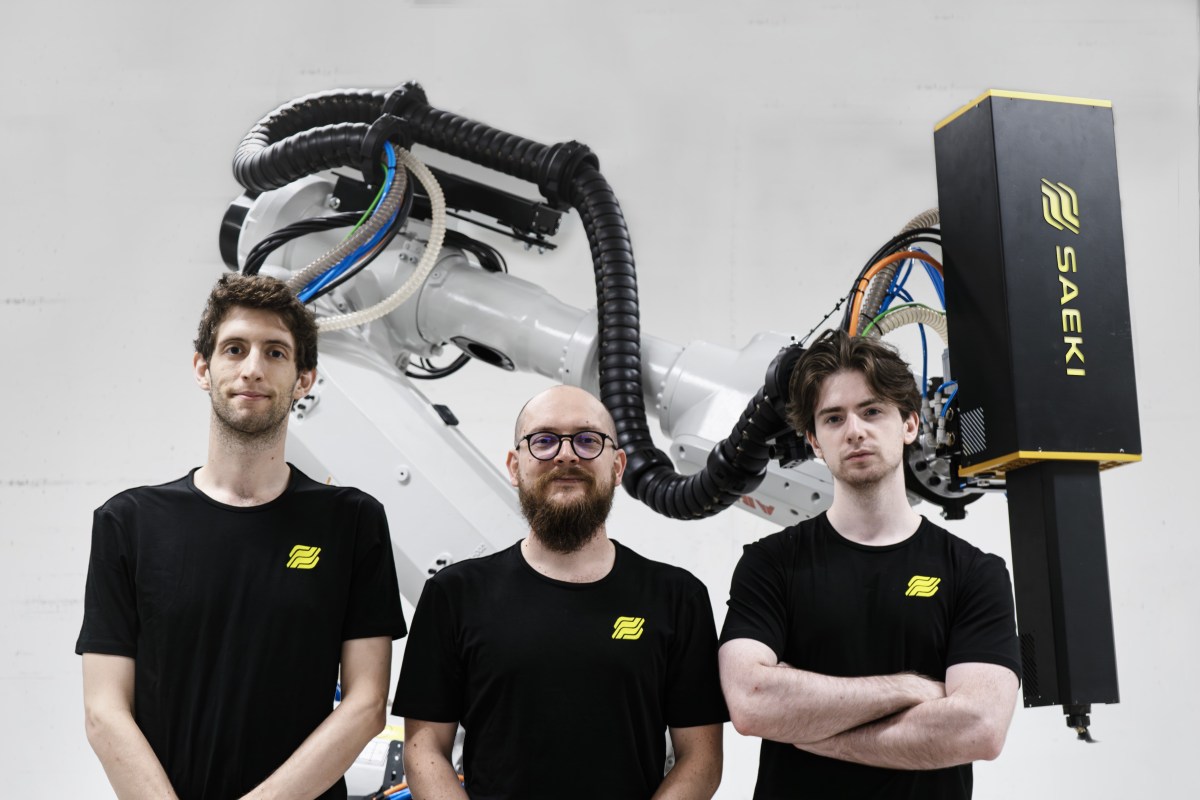
SAEKI’s “microfactories” help large manufacturing scale up
The architecture, engineering and construction industries involve giant concrete molds that are expensive, slow to manufacture and often only used a few times before being disposed. Robots-as-a-service startup SAEKI says its tech not only makes creating these molds faster, but also more cost-efficient. The Lupfig, Switzerland-based company is building what it says will be fully automated plants with industrial robots that use 3D tech to create components like aircraft wings and construction site installations.
SAEKI launched from stealth today with $2.3 million in seed funding led by Wingman Ventures, along with participation from Vento Ventures, Getty Capital and angel investors.
It is currently building its first production hub, which will have industrial robots that are capable of combining digital manufacturing methods, including 3D printing, milling and inspection. SAEKI says the robots each act as “microfactories,” which means they are self-contained units that can do all manufacturing steps.
SAEKI was founded in 2021 by Andrea Perissinotto, Oliver Harley and Matthias Leschok. Perissinotto told TechCrunch he became interested in manufacturing when he was a child, learning metalworking at his uncle’s workshop and building his first 3D printer when he was 12. He met Harley while building a large 3D printer for the maker space at ETH Zurich, where they were both studying, and they began working with Leschok to combine 3D printing and industrial robots.
The three were completing their studies during the pandemic when Perissinotto decided he wanted to leave academia and become an entrepreneur. SAEKI was founded in February 2021 to combine robotics with 3D printing, machining and inspection. During that process, Perissinotto said he and his co-workers learned that 3D printing for large items, like wind turbine blades, airplane and car parts, was still early in development and not at industry quality and scale yet. They decided to focus their new startup on the issue by creating fully automated factories with independent robotic cells that customers can book.
Want the top robotics news in your inbox each week? Sign up for Actuator here.
SAEKI produces the large components needed by industries like construction, aerospace and automotive, without needing to retool their machines. This is a time- and cost-saving advantage for components that are only used a few times during the building and manufacturing process.
For example, when constructing buildings out of concrete, builders first need a mold called a “formwork.” Unless it is being used for something standard, like a flat wall or ceiling, special formwork needs to be created from scratch. Typically, they are built by hand out of wood and scrapped after building is completed. SAEKI’s solution is to use recyclable thermoplastics that are 3D printed and processed by one of its robots and delivered to construction sites.
It also plans to work with the composites industry, which builds the lightweight but strong parts found on airplanes, cars and bikes, among other things. These parts are usually made in complex molds created from metal or composite materials. Perissinotto said this creates a bottleneck for companies because the molds are expensive and need a long time to build. SAEKI’s goal is to reduce lead time costs and use their tooling processes to enable companies in the composites industry to have faster hardware production cycles.
Since SAEKI’s robots act as “microfactories,” this means its customers do not have to purchase another new machine or take up more floor space in their facilities. Perissinotto said this is why SAEKI decided to use a robots-as-a-service business model, since that allows customers to just purchase the amount of time they need with a machine.
SAEKI is currently finalizing its first pilot projects in the architecture, engineering and construction (AEC) sector, with customers using its 3D printed formwork to create custom concrete elements. Its target AEC clients include construction companies, pre-casters, interior designers and architects.
Perissinotto said SAEKI is already generating revenue because of its pilot projects. It is building its first factory in Switzerland, but its robots are already operational and have already been producing parts for the last few months.
In terms of competition, Perissinotto said additive manufacturing has been a “prominent topic” for years now, and even though there has been significant advancement in tech, market acceptance has not fully matched that progress, due in large part to the cost of the machinery involved. Even though additive manufacturing has gained some traction in the industrial market, it is still in the early stages when it comes to large-scale applications, he added. Companies that offer machines for large-scale additive manufacturing include CEAD B.V., Caracol AM and Therwood Inc, but Perissinotto said SAEKI’s customers want a different approach.
“What we consistently hear from people and companies is a desire for faster more sustainable solutions for their parts,” he said. “Merely offering savings through a multi-million dollar machine that requires extensive space and additional resources, including hiring personnel well-versed in new processes and materials, is not appealing to them.”