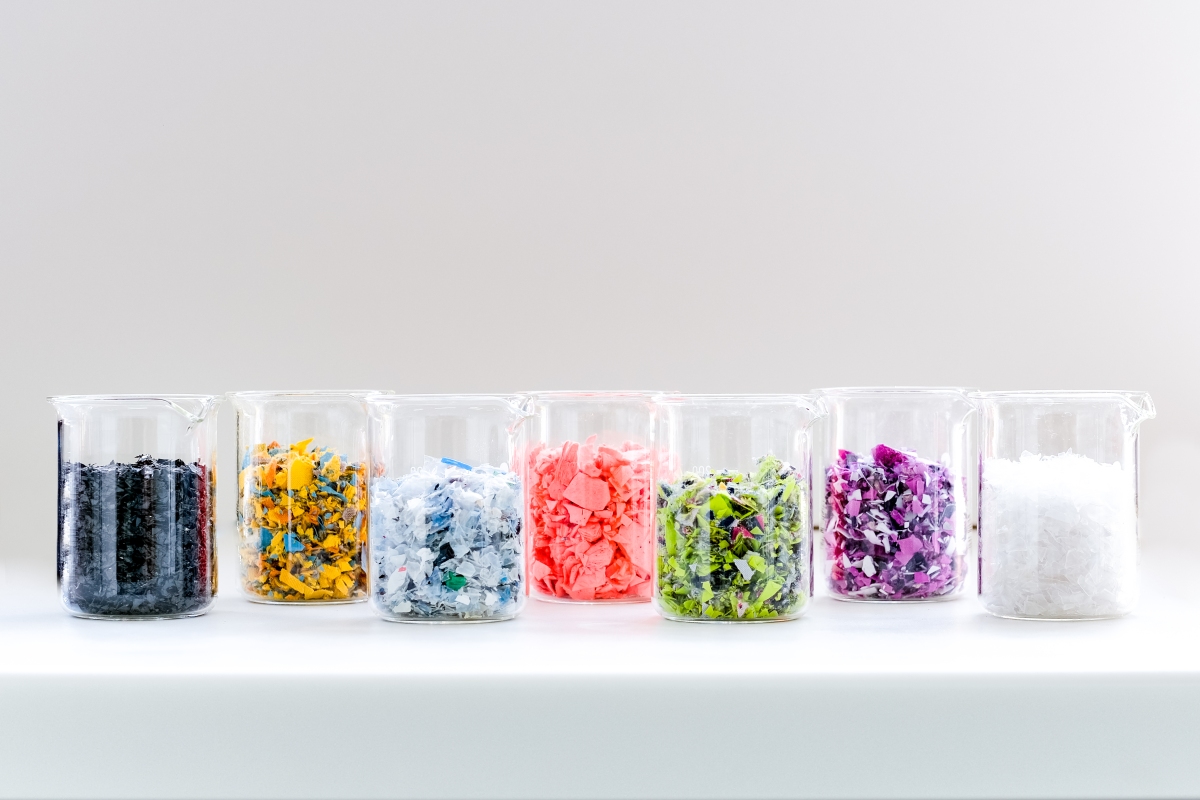
DePoly keeps hard to recycle plastic from ending up in landfills
About 400 million tons of plastic are produced each year, but less than 10% is recycled, with most of the rest ending up incinerated or in landfills. One reason is that it is difficult for conventional recycling processes to handle contaminated plastics, like those that are made up of several different types of plastics, combined with other materials or just plain dirty. DePoly, a deep tech startup, has developed a process that is able to tackle complex plastic streams and turn plastics back into raw material without affecting quality. The Swiss-based startup announced today it has raised $13.8 million in seed funding.
The round was co-led by BASF Venture Capital and Wingman Ventures, with participation from other investors like Beiersdorf, Infinity Recycling, CIECH Ventures and Angel Invest.
DePoly’s chemical recycling tech converts all PET plastics and polyester textiles back into their main raw chemical components, which are then sold back to the industry to make new items. DePoly says items made from its raw material are virgin-quality.
The company currently operates a pilot plant that can process 50 tons per year of complex PET or polyester plastic streams. It serves industries including post-consumer packaging, textiles, fashion and post-industrial streams. DePoly is building a showcase plant with a capacity of 500 tons to demonstrate its tech at commercial scale, and already has five customers, ranging from fast fashion brands, sporting good brands and packaging users to resin producers.
DePoly was founded in 2020 by CEO Samantha Anderson, CTO Bardiya Valizadeh and CSO Christopher Ireland, and now has a team of 13 people. In the years before launching DePoly, the three moved to Switzerland to work on their PhDs and post-docs. Anderson told TechCrunch that there were a lot of articles being published about issues like microplastics in people, growing plastic patches in the ocean and animals washing up on shore with microplastics in their stomachs.
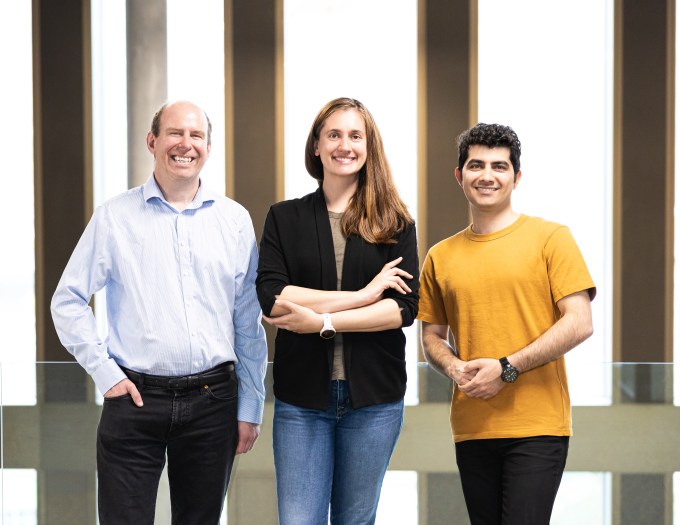
DePoly founders Christopher Ireland, Samantha Anderson and Bardiya Valizadeh
“For us, all this was quite alarming, particularly that companies seemed not to care about solving the problem now, not in 10 to 15 years,” Anderson said. “So we decided that we wanted to tackle the plastic problem, using chemistry and the skills we had developed during our degrees, with the aim of if we could make it work, to spin a company out and tackle the problem faster than others were moving.”
Conventional plastic recycling means things like bottles and food packaging made of PET and other plastics are brought to a recycling facility, then sorted into colors, cleaned, melted and turned into rPET pellets. But if they are too dirty, mixed with other plastics or in fabric or fiber form, they usually get incinerated or dumped into a landfill, Anderson said. There are also limits to what can be recycled because of health and food safety standards, which means the majority of plastic produced is destroyed or thrown away, and new plastic has to be made from crude oil.
DePloy’s chemical recycling tech operates at room temperature and standard pressure, and does not need plastics and materials to be washed, pre-sorted, pre-melted or separated. This means it can be used to recycle PET and polyester that don’t make it into conventional recycling systems, including mixed plastics, mixed colors, dirty plastic waste streams, fabrics and fibers. PET is converted back into PTA and MEG, its original two monomers.
Anderson explained that DePoly has a B2B model, connecting users of complex plastic waste, like blended polyesters, multilayered PET items or PET items that are too dirty or chemically contaminated to be introduced into the mechanical recycling process, with people who produce virgin quality PET items from oil because of limited accessibility to sustainable chemicals like PTA and MEG. DePoly’s tech allows one side to get rid of PET and other plastic waste, and the other side (or the producers) to have access to the original, sustainable chemicals that make up those items, creating a circular economy for plastics.
DePoly can also do content recovery. For example, it can recover PP or cotton from PP/PET combos or cotton/polyester blends. Anderson said this is because of the low temperature of its system, because it doesn’t melt polymers. The startup is also scaling tech for polyurethanes (PU), polylactic acid (PLA) and similar polymers like PBT.
As an example of how DePoly’s chemical recycling process has been used, Anderson said its worked with customers in the sporting goods industry that have polyurethane blended polyester items. The polyurethane content means those items would usually be discarded, but DePoly is able to fully recycle them and is now scaling its tech to recover the polyurethane portion.
Anderson cites startups Carbios, Gr3n and Ioniqua as other startups that are doing similar work with plastics, and says she thinks “the tech they’ve developed is really neat.” The main way DePoly differentiates is the reaction that occurs during its recycling process, the product output in Ioniqua’s case, the temperature required for the reaction and the contamination threshold allowed. “In our case, we’re lower temperature, produce the same monomers that make up PET and to our understanding have a higher contamination threshold versus others.”
In a statement about the investment, Wingman Ventures principal Antonia Albert said, “We are extremely proud to support DePoly since day one on their journey to tackle this planetary crisis to clean our oceans and landfills from plastic waste and to welcome leading investors from the chemicals, recycling, climate- and deep tech space on board to build the global leader for the sustainable plastics recycling.”